Best Ways to Deal With Concrete Cracks
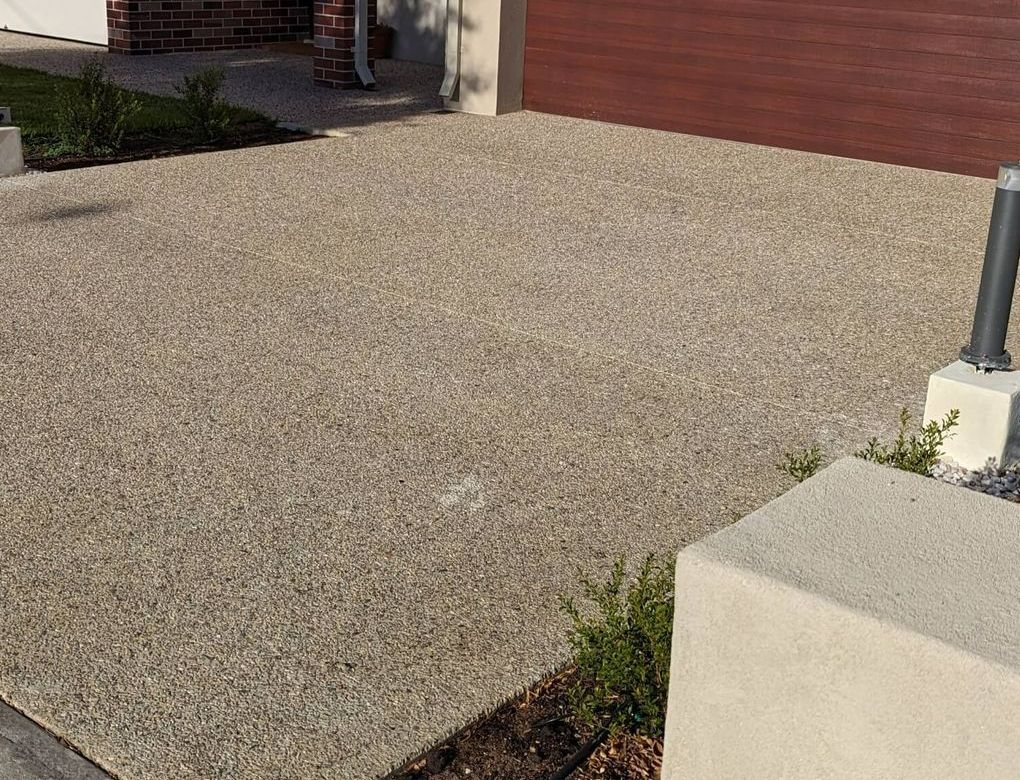
Whether you're dealing with concrete cracks in your home or business, there are a few ways you can address the problem. From surface protective coatings to stitching, there are several methods to choose from.
Stitching the Cracks
Using crack stitching to repair concrete cracks can improve the look of a home or structure and can help prevent future damage. In addition, this technique is a permanent solution to cracked masonry. It can be used to treat a wide range of concrete and brick cracks.
Depending on the condition of the concrete, stitching may be the best way to repair a crack. Stitching involves drilling holes in the crack and fixing the crack with a rigid resin material. Several methods can be used to stitch the crack, including epoxy injection and gravity filling.
Injection of epoxy is one of the most common ways to stitch the crack. Epoxy is injected into the crack and then a liquid adhesive is applied to the top of the crack. The adhesive creates a strong bond between the two surfaces. The material used to inject the epoxy should be suitable for the crack. It is important to ensure that the joint will accommodate any movement that the crack will experience.
Another type of cement crack repair method is called grouting. During this procedure, a liquid adhesive is injected into the hole. The holes are usually 7/8 to 4 inches (20 to 100 mm) in diameter. This method is generally used in bed joints and is a quick and easy way to repair a crack.
Another popular type of concrete crack repair method is called cross stitching. This process uses deformed tie bars to maintain the aggregate interlock and provide added strength to the crack. The bar is drilled at an angle and is inserted into the holes. This method is usually used to fix longitudinal cracks that are in good condition. However, it can be used to repair transverse cracks as well.
The third commonly used method is called U-bar stitching. This technique is used to repair a crack that is wider than the spacing of the rebar stitching materials. A metallic U-shaped wire is then passed through the holes. The bar is then anchored with non-shrink grout.
Other techniques for stitching the crack include routing and sealing. This is a procedure that involves cutting a groove in the cracked concrete and injecting a material that will fill the crack. The material can be made from asphaltic materials, polymer mortars, or any other suitable material. The procedure is not appropriate for active leaks but can be used for wet cracks.
The fourth and final method of stitching the crack is to use carbon fibre laminates. These are stronger than traditional rebar dowels and are also faster to install. They can be used to stitch a crack on a swimming pool deck, patio, driveway, garage floor, or poured concrete foundation wall.
Despite the advantages of using carbon fibre, it is important to note that the holding strength of the stitches is directly proportional to the surface bonding area. The longer the surface bonding area, the stronger the bond between the rebar and the concrete.
Plastic shrinkage cracks
During the construction of a concrete structure, it is imperative to take steps to prevent the formation of plastic shrinkage cracks. These cracks can have detrimental effects on the durability of the structure. It can even affect the appearance of the slab.
Plastic shrinkage cracks are usually visible within three hours of casting the concrete. They occur most often on the surface of the concrete. They can range in length from a few millimetres to a few meters. They tend to run parallel to the casting direction. However, they can also extend through the full depth of the structural slab.
Plastic shrinkage cracks are caused by evaporation, which occurs when the moisture content of the concrete decreases. This condition can be aggravated by harsh environmental conditions, such as wind velocity. It can be prevented by controlling moisture loss. One effective way to do this is by misting the slab. Another method is to cover the area with a polythene sheet. This can reduce evaporation rates and protect the concrete from excessive drying winds.
Aside from evaporation, other factors can contribute to the formation of shrinkage cracks. These include formwork, changes in depth, and changes in cross-section. Incomplete consolidation can also cause fold lines.
The most important factor influencing the formation of shrinkage cracks is the water content in the concrete. It is a good idea to measure the relative humidity of the environment to find out how much moisture is being lost from the concrete. This can help you to determine the temperature curve of the concrete.
The evaporation rate nomograph is a handy tool for measuring evaporation rates. Several factors can influence the evaporation rate, such as the temperature of the environmental chamber. It is a good idea to use a climate-controlled chamber when controlling the environment. This allows you to control the temperature and relative humidity, which can help you prevent the formation of plastic shrinkage cracks.
A microscope can be useful to examine the features of the crack. The most obvious feature is that the sides of the crack have been distorted by tensile forces. The crack's interior surface will have a multitude of tiny angular planes. Occasionally, the aggregate particles within the crack may be partially broken. These are the least likely to be caused by plastic shrinkage.
Besides the evaporation rate, other factors that contribute to the formation of shrinkage cracks include weather conditions, finishing operations, and pouring methods. The amount of moisture that evaporates from the concrete will determine how long it takes for the shrinkage to stop. If the concrete is not cooled down enough, the internal temperature will be too hot, which can make the cracks worse.
To eliminate the occurrence of shrinkage cracks, it is best to cover the concrete as soon as possible. The most effective solution is a polythene sheet that can be suspended clear of the concrete surface.
Surface protective coatings
Providing concrete cracks with surface protective coatings is a great way to protect the structure from the damaging effects of water and other aggressive substances. These coatings act as a physical obstacle preventing the penetration of harmful agents into the concrete and also help to extend the useful life of the structure.
For the best protection, it is recommended that the concrete surface be impregnated before the application of the protective coating. A variety of impregnation systems are available, including silicone preparation, silicon sealants, and epoxy resin. Depending on the specific requirements of the site, the type of substrate, and the intended use, the optimal treatment can be determined.
Crack-bridging capability is a property of the coating and is closely related to the type of protective material used. In general, the polymer-cement (PMC) or epoxy-bitumen (EB) systems are better at covering larger cracks than the aqueous silanes and sealers. However, in a test comparing these two, the acrylic and epoxy systems showed a lack of elasticity.
AQUASEAL(tm) UB III is a high-performance polyurea elastomer invented for concrete surface protection. It is a spray-applied product that expands over 300% of its original volume during the application process. The elastomer forms a seamless membrane, sealing the pores of the concrete and reducing the surface prep time. In addition to its excellent performance in protecting concrete, the product has a wide range of applications. For example, it is ideal for spot repairs of existing coatings and for repairing control joints and cracks in floors and decks.
In addition to the above properties, emerging concrete protection solutions include products with excellent freeze-thaw resistance, low chloride permeability, and rapid setting times. Some of these products exhibit electrolytic conductivity, which acts as a skin sensor for structural health monitoring. This feature is still in the experimental phase.
For the best protection, it is a good idea to find a system that complies with EN 1504-2, the standard that outlines the key criteria for selecting a protective coating for reinforced concrete structures. The standard covers both the physical and chemical resistance of the coating, as well as moisture and carbon dioxide control. In the case of epoxy-bitumen and acrylic elastomeric-based treatments, the resistance to carbon dioxide is over 50 m.
The quality of the cover is especially important for concrete surfaces because the curing process can produce substantial amounts of water. If the cover is poor, this can accelerate the corrosion process. Therefore, it is a good idea to choose a surface coating that can accommodate both the thickness of the missing cover and the cracks present on the surface. A suitable covering can increase the longevity of the structure and reduce the risk of corrosion of steel reinforcement.
The most important property of a surface treatment is the ability to bridge the cracks in the substrate concrete.
We hope this article has given you some helpful tips to address your concrete crack issue. If you have any more questions about concrete crack repair or would like to schedule a free estimate, please contact us anytime at 03 9118 0604. Thank you for reading, we always appreciate your time and attention!
Contact Form
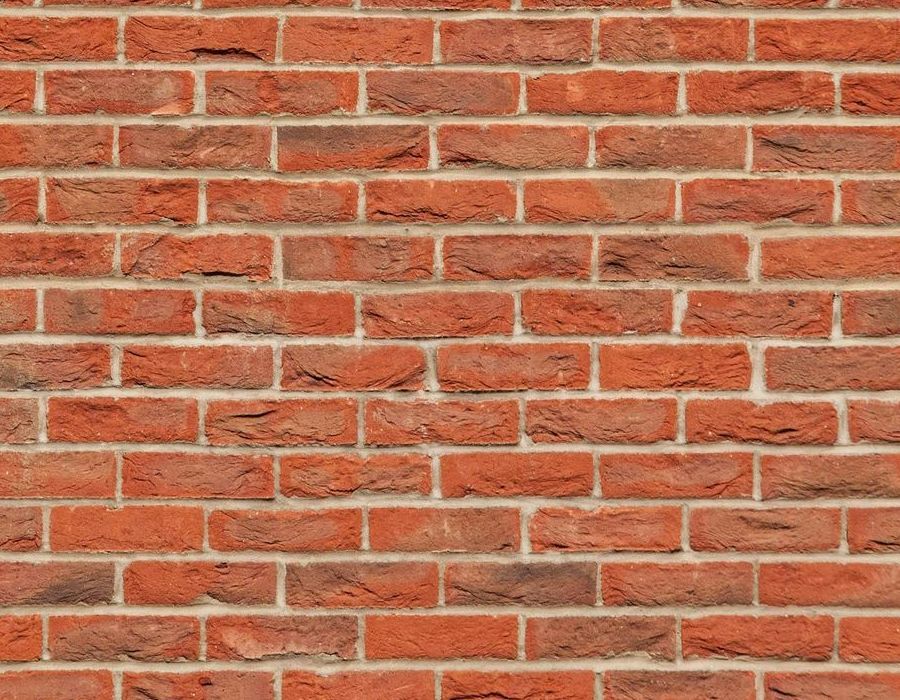
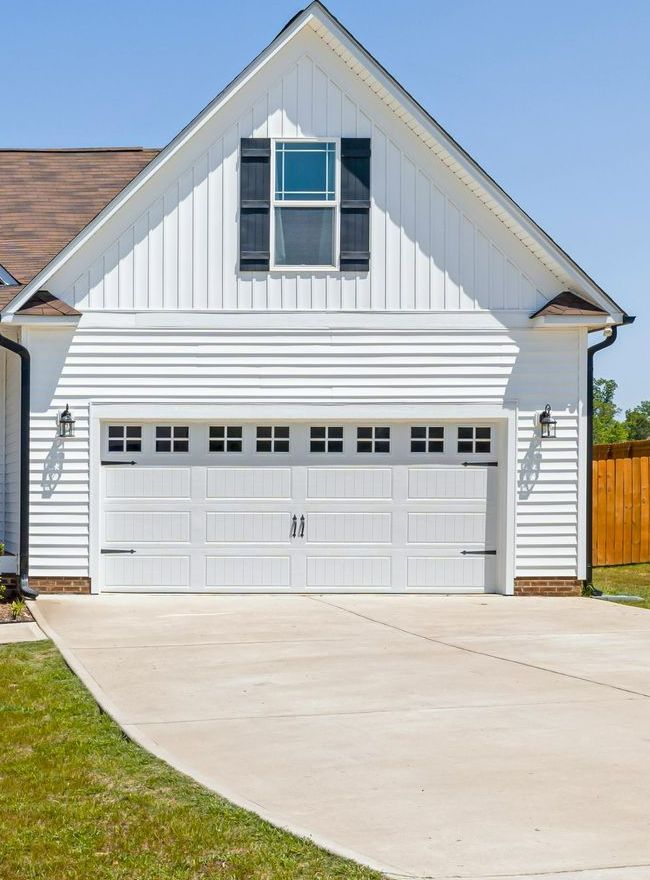
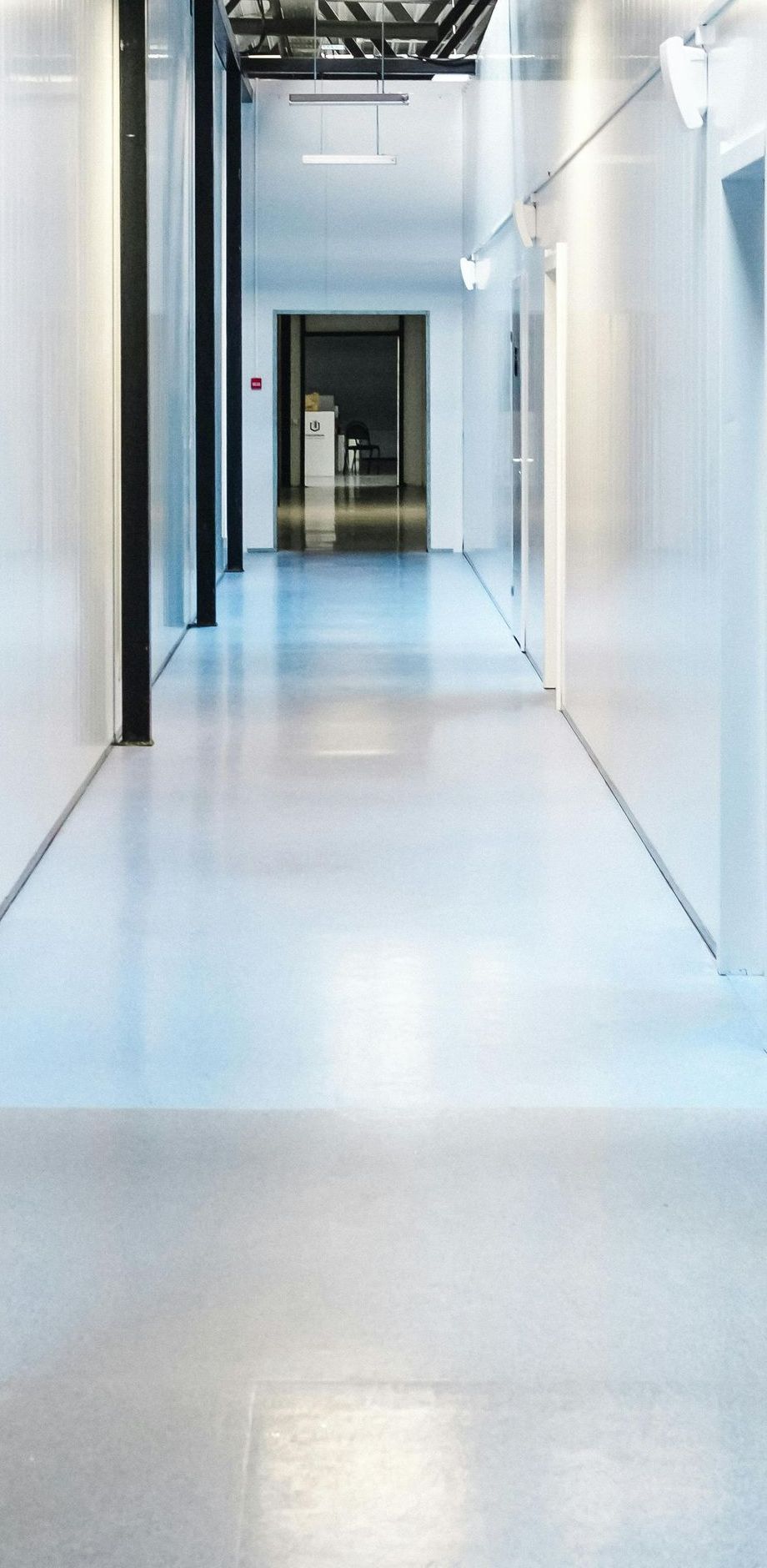
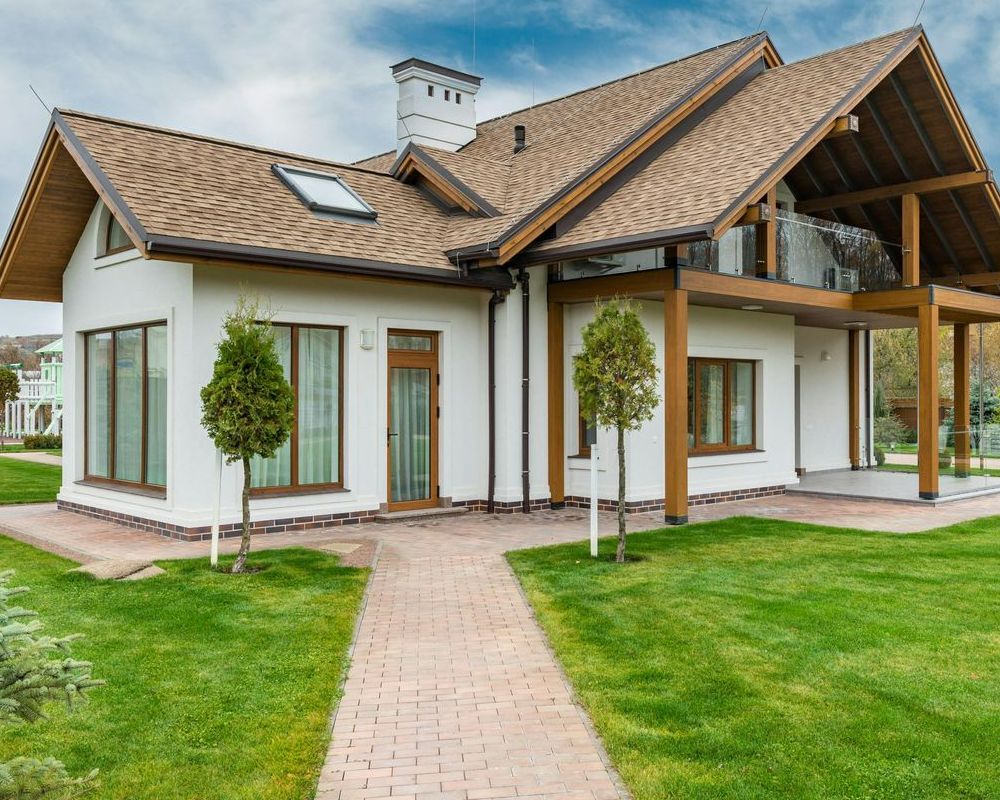
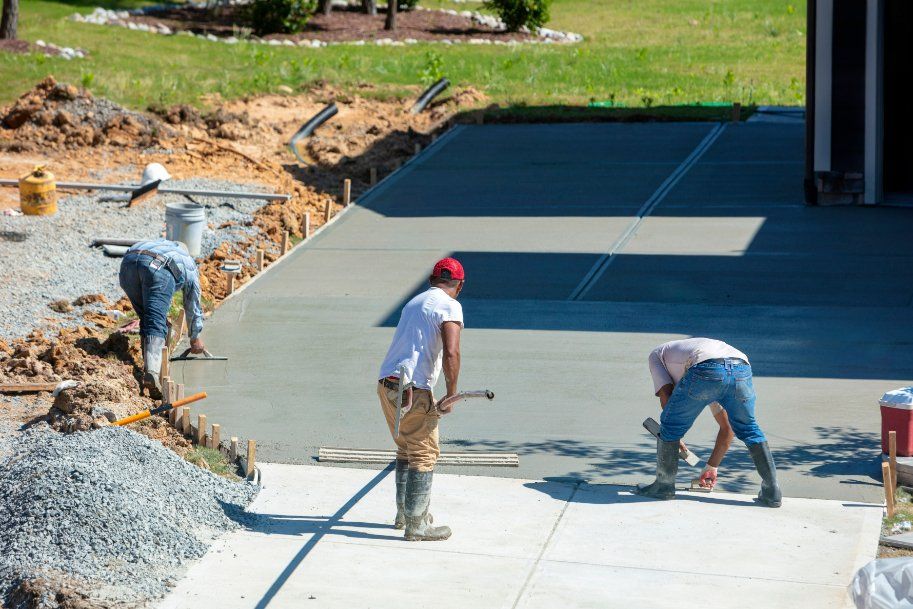
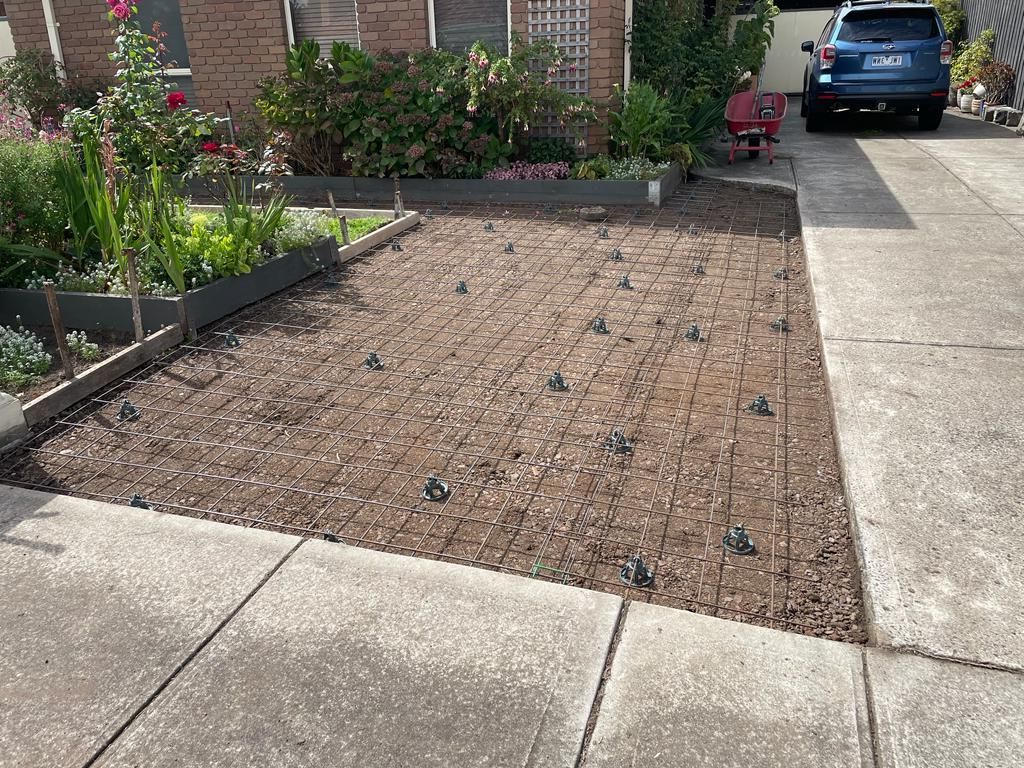
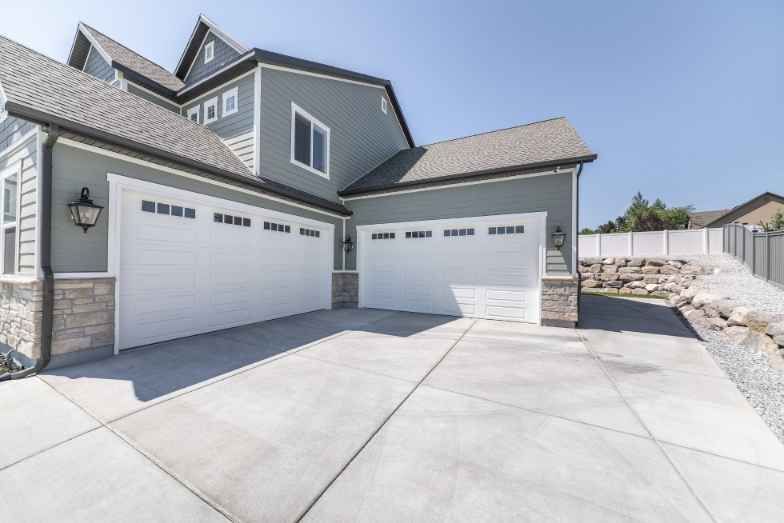
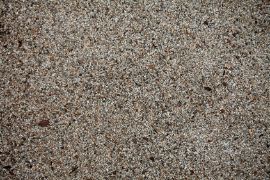
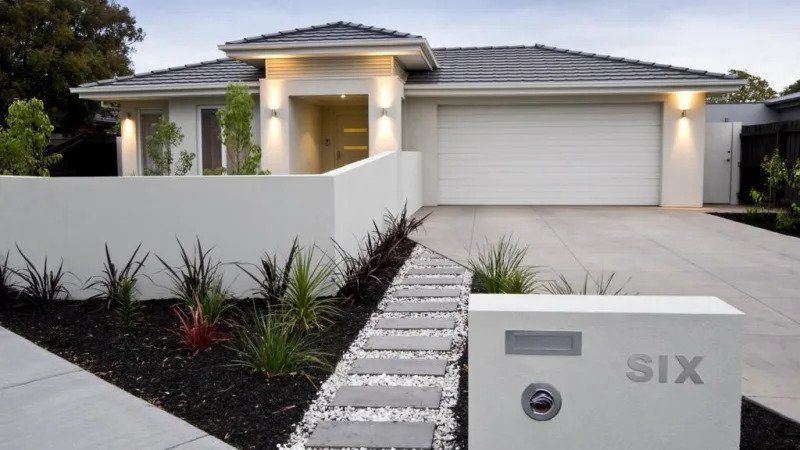
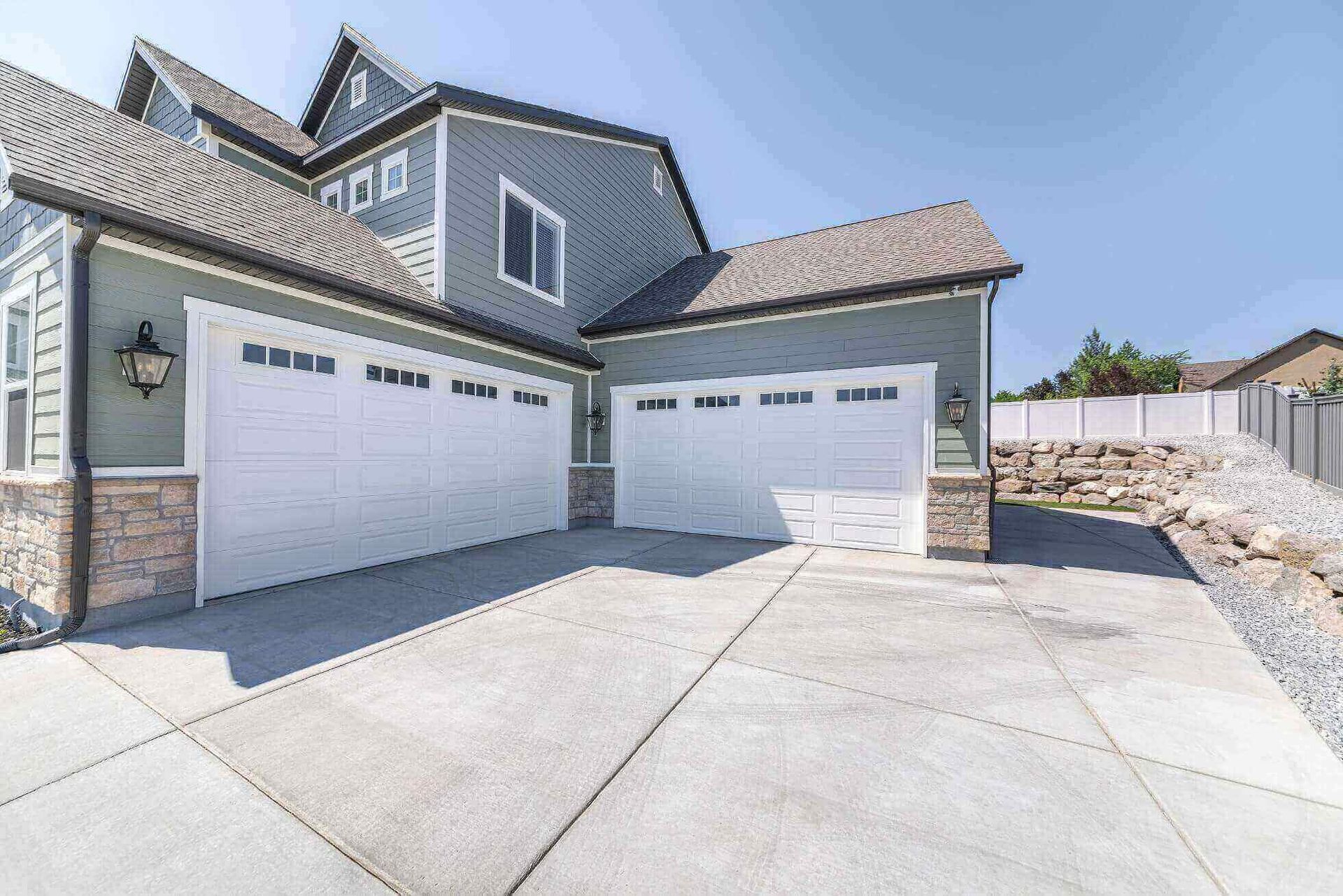